- Laboratory information management solution (LiMS)
- Enterprise Resource Planning (ERP)
- Visitor & Employee gate pass Management System
- Vehicle Control system
- Potent Digital Signage
- Management Information system (MIS)
- Watch Tower
- Real time monitoring of extrusion process
- Potent ABT system for power sector
- Potent Material Live Tracking
- Industrial automation 4.0 Implementation
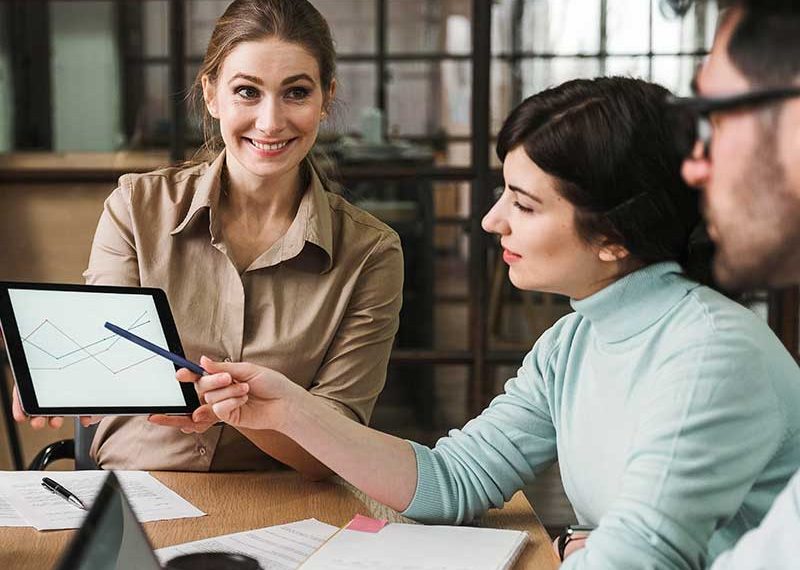
Product overview
Manufacturing environments, in general, require raw materials and work in process to go through a series of different assembly stages. The subassemblies or raw materials are passed from one location to another in totes or containers. Leveraging human employees to check the accuracy of every assembly line resulted in more time consumption, increased labour wages and human errors. This is when potent material tracking systems came in to save the day.
With Barcode or QR code enabled tracking systems, each tote or container can be uniquely examined by virtue of the tags in them. As these works in progress pass from one station to another, the tags record the status of the components. Barcode or QR code based potent tracking system can immediately report if any deviation from the ideal process is encountered. This way, even the tiniest mistakes can be spotted and corrected in the initial stages and companies get the ability to avoid pricey mistakes and scale down manufacturing errors.
The advantage of tracking work in progress extends beyond making the production status visible. The data can be used to identify factors like shelf life of the finished goods, depletion of raw materials, things that the defect products have in common and so many useful things to prevent scenarios like bottleneck, supply-demand gap etc
Space in the production floor is limited and has to be used optimally. Potent tracking systems determine if there’s any space wasted on the floor and help you decide how you can utilize it. Shelf-life expiry is also one of the major problems when it comes to manufacturing. Manufacturing tracking systems determine the expiration dates of products and lets you know which ones to give away first.
Human errors have a lot to do with product quality which is why most of the systems in manufacturing are automated. Potent tracking systems perform quality checks throughout the manufacturing process and send real-time data to both management and the line workers. This makes sure that no error is left unnoticed, and no product is taken past the erroneous stage without being fixed.
Potent tracking systems is all about tracking, measuring and optimization. Managers use the precise output of these system to make sure that none of the workers are ideal and efficiently plan the optimization of machine downtime. Potent material management solution help the management identify the movement of outbound goods. This way manufacturers can easily fix the supply-demand gap.
Continuous monitoring ensures quality control from picking the raw material to dispatching the final product. This helps us maintain the accuracy of inventory levels and helps us recognize the labor and overhead costs. Material tracking systems ensure that the materials for through every stage of manufacturing. This will eventually prevent returns due to manufacturing defects. Optimization of labor hours and machine downtimes male the production more pocket friendly. Also, prevention of misdirected resources can save you a lot of money.